[ad_1]
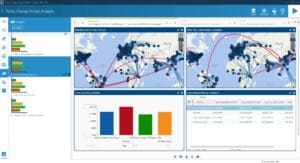
Imagine you’ve just received the job offer of your dreams. The company is willing to relocate you thousands of miles away from home and your family is in full support. The interview process is over, but more challenges are ahead. Which school are your children going to attend? Are you going to rent a house or an apartment? Should you buy, rather than rent? Do you get one car or two cars? Gas or electric? And what about those jiu-jitsu classes you’ve wanted to take for such a long time?
As you’re working your way through these questions, you’re looking to minimize your commute while maximizing the quality of life for you and your loved ones. If you have been through this process at least once, you already have a good idea of what supply chain design is about: optimization.
When most people hear the word “optimization,” they immediately think about minimizing costs. But optimization is much more than that! A company can choose to maintain a high level of costly inventory to ensure short lead times, and a family can decide to live farther away from work and school but buy a bigger house. Optimization is about increasing value, and the exact meaning of this can vary from company to company, and from family to family.
Let’s continue with this analogy. Last year multiple companies needed to urgently relocate their employees and their families from Russia and Ukraine. Think about these relocations! These companies needed to find answers to all the same questions about accommodation, commuting, and recreation. Their time frame was short and resources limited. Moreover, this exercise might need to be repeated several times depending on how the war proceeds. At some companies, these relocations involved moving groups of different sizes from different offices with hundreds of possible destinations. The groups themselves were non-homogeneous with people of different ages and interests. Should these companies approach relocation as a brand-new problem every time? Should the company come up with a one-size-fits-all solution?
Neither! Ideally what should be done is to invest the time to build a repeatable process that will help give recommendations based on input parameters. For it to be an optimal solution, a mathematical model needs to be used. That model can then be used to analyze every new situation that arises. The model will help a company find a solution that is best for their relocated employees as a whole. This means that some group members will have to commute longer or will not get a house with all the amenities, but collectively the relocation can be set up as optimally and as quickly as possible.
Let’s replace “people” with “customer orders”, “family members” with “SKUs” and “housing” with “distribution locations” and you have the components of a common supply chain design problem. Supply chain design can help you find answers to a wide range of questions, but most companies begin their journey with one question: “Which distribution centers should I assign to which customers?”
To solve this problem, we’ll need to do three things: understand the data, aggregate the data, and define the constraints.
First comes the data and how well we understand it. Let’s begin with customers: how many do we have, how often do they order, and what are the typical order quantities and patterns? Do we have a demand forecasting tool in place and, if so, how good is that forecast?
Once we have a good grasp of that piece, we can move on to the second step. We will now start generalizing – in other words, aggregating the data. The purpose of data aggregation is, on one hand, to minimize the number of records you’ll be working with and, on the other hand, to reflect critical business patterns: order prioritization, customer segmentation, sourcing logic.
If we have 1,000 customers in reality, we might use only ten customers in the model when we aggregate data. We will consolidate their characteristics to create representative groups. For example, we can have “Texas Small Volume” customers and “Florida Peak Season” customers, or “East Coast High Margin” customers and “Carolinas High Priority” customers.
Data aggregation is the heart of supply chain design, and every company’s business requires a slightly different approach. For example, a model for a company with twenty distinct customers with unique buying patterns, who are located all around the world, might not require aggregation at all. However, this model would aggregate the details of the ten thousand SKUs that are stocked and shipped.
At the same time, another company might have twenty suppliers with similar pricing strategies, who supply the same raw material. Because of these similarities, they might group them all together in the model. However, they could decide not to aggregate their SKUs because of the vast difference in production time and margins.
Note that we haven’t designed a supply chain model yet, but we have already enhanced our understanding of the business!
We can use this same method to represent customer orders, suppliers, manufacturing sites, warehouses, transportation assets, and all other agents that you have in your company’s value chain. After we aggregate data for all of these agents, we end up with a certain data structure: the building blocks for our supply chain model.
Finally, when aggregated data is available, analyze internal processes and define constraints. Can every customer get products from every warehouse? What are the accepted lead times in the industry? How easy is it to open and close distribution centers or move products across manufacturing facilities? What is your company’s strategic response to a sudden surge or a drop in demand? Thinking through these questions helps finalize your model.
Once you have a model in place, it becomes possible to play out various events and find the best way to react. For example, we can now model adding or removing a warehouse, increasing capacity at our production lines, adding more trucks to the fleet, and basically any other change you can think of. Moreover, with a pinch of advanced analytics we can start predicting the future events and taking preemptive action.
In sum, Supply Chain Design is the process of modeling your business activity as a set of rules. Rather than simply minimizing costs, supply chain design allows you to maximize value.
About the author:
Marianna Vydrevich is an expert in supply chain design and an active member of Coupa Supply Chain Design community. She is currently the Manager of Advanced Analytics at GAF, North America’s largest roofing and waterproofing manufacturer, where she oversees network modeling as well as other projects across operations.
[ad_2]
Source link