[ad_1]
28th June 2023
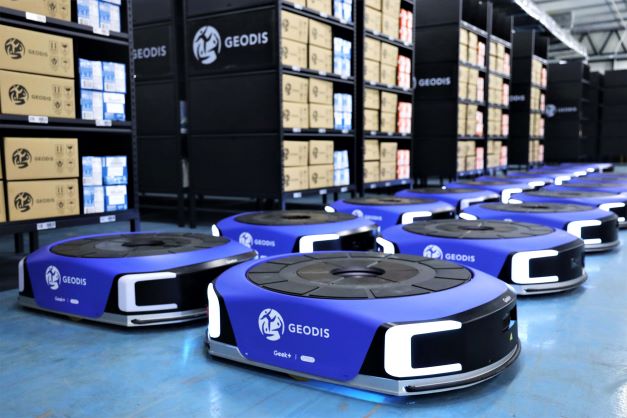
Geodis VP of Engineering, Antoine Pretin, says that technology is rapidly becoming a key success factor in ecommerce logistics. Speaking at the Deliver Europe conference in Amsterdam, Pretin said automation is better than manual handling because costs are controlled after installation, whereas labour costs can rise, as they are now, thereby impacting the running costs of the warehouse.
“Automation increase accuracy and quality,” he said. “In automated distribution centres you need a strong and stable team, but less training and management. Square metre optimisation is achieved by using the full height of the building.” Employee satisfaction can also be good, he argued, as automation and robots are considered to be both fun and safe.
“The length of a third party logistics operator’s contract must match the investment and payment for technology,” he advises, “or you can rent robots. Larger DC system integrations can take two years to complete as materials handling suppliers are very busy.”
Pretin says that shared user warehouse facilities are very challenging. His preference is for standardisation, i.e. all Geodis warehouses would be the same, with the same technology. “I prefer to have one AMR or AGV supplier, so they can be moved from site-to-site if required.” There are around 250 suppliers currently.
ROI
“It’s all about customer-orientated solutions,” he emphasised, “we start with an understanding of what the customer does, then design the facility and project accordingly. Offering flexibility is important in ecommerce, for example in being able to reduce the number of cartons.”
What about the return on investment of automation? “Automation prices are rising. ROI varies depending on the number of shifts operated. But when you can’t hire staff there’s no alternative to automation and AMRs. I expect costs to fall as we get to mass uptake.”
[ad_2]
Source link