[ad_1]
Traditionally, planning processes are designed to serve specific time horizons – sales & operations execution (S&OE) is used for short term horizon, sales & operations planning (S&OP) for the mid-term horizon, and integrated business planning (IBP) for long term strategic horizon. In its ideal form, supply chain planning should help leaders balance customer service with profits and even cash flow. Increasingly it is recognized that the executive planning meetings, that typically take place once a month, should be chaired by a top floor executive – a chief financial officer, chief operations officer, or even chief executive officer.
Research by McKinsey concludes that all too often IBP is an ineffective process. “In a survey of 54 senior executives, only about one in four believed that the processes of their companies balanced cross-functional trade-offs effectively or facilitated decision making to help the P&L (profit and loss) of the full business.”
There is a known problem for manufacturers in synchronizing their supply chain. The shop floor to top floor disconnect reflects the difficulty of synching the plans finalized in an integrated business planning executive meeting with what the shop floor is capable of manufacturing in the short-term time planning horizon.
I talked to Chris Botha, a senior vice president at UST, about this problem. UST is a global consulting and systems integration firm with over 30,000 employees. Mr. Botha’s firm, SCM accelerators, was acquired a few years ago by UST. Mr. Botha does a lot of supply chain planning work implementing SAP supply chain solutions.
I mentioned to Mr. Botha that I had recently talked to a company that had implemented a supply chain planning solution, and then abandoned it. The problem was that when the planning solution spit out recommendations, and someone in sourcing or someone on the factory floor looked at those recommendations, they just did not believe them. Fewer and fewer planners were willing to use the application until there was no point in keeping the application. This is known as the “black box” problem.
Mr. Botha replied, “I hear that a lot.” Mr. Botha’s view was that certain supply chain solutions are more friendly than others. Demand planning or SAP’s S&OP solution are easier to use. Meanwhile, inventory optimization and production scheduling are more of a black box. Users need to understand that the algorithms powering these solutions have been around for some time and are proven. In other words, trust more, question less.
Customers that implement inventory optimization or production scheduling and then turn it off, Mr. Botha argued, often have a lower level of supply chain maturity. “They haven’t even done proper supply-demand matching up front. They haven’t done roughcut capacity planning.” Roughcut capacity planning is also called supply planning.
Immature customers do roughcut capacity planning in a manner that is not at all accurate. They may have a sense that a plant can produce 20,000 units of a product in a week. Where this estimate came from, no one can really say. If these rough rules of thumb are used, poor planning is the result. When the plan gets dropped to the plant, the plant can’t produce that quantity of items nearly as quickly as thought. The plan did was incapable of considering things like labor availability, machine throughput, and other real-life constraints.
The model used to balance demand with supply in the integrated business planning meetings needs to be constraint-based. “To really do IBP properly, you’ve got to have all the basics right. Your inventory levels in the factory are right, your routings are accurate. Your labor times and labor standards are correct,” Mr. Botha explained. If these things are in place, application abandonment is much less likely to occur.
The supply planning model can include, at a higher level, the throughput and constraints of several factories. Mr. Tushar Bhalla, the chief technology officer at CloudPaths, believes that COVID taught many companies that this higher-level constraint-based model also needs to include warehousing, transportation, and sourcing constraints. CloudPaths implements solutions from SAP with a significant portion of their practice focusing on SAP’s supply chain planning solutions.
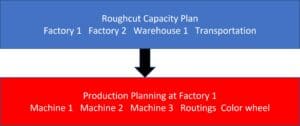
Mr. Bhalla also believes “switchable constraints” increase supply chain agility. An example of switchable constraint would be a factory that needs to close. The base model would assume that all factories are producing goods. But if a factory does need to close for some period, that constraint is switched on. Then different scenarios for attempting to balance demand with supply can be considered.
Once a constraint-based supply planning solution is in place, it is possible to put in detailed production scheduling. Here the model gets more complex. One example of this is the use of color wheels in the model. If we must produce products A, B, and C, then we should produce A first, then B, then C. Doing it this way will minimize setup times. Further, are two people needed to operate a machine? Can it be any two people? Or is a specific skill set required? Those that have modeled production scheduling know that the process can get very complicated, very quickly.
Once manufacturers climb up the maturity curve and have developed a capacitated roughcut model, it is reasonable to expect that the planned output over some period of time – say a two-week planning horizon – is achievable. Two weeks gives the scheduling application more opportunities to create sequencing and setup synergies. At the end of that biweekly period, the variance between the top floor plan and the actual output from the factory floor will be minimized.
However, the granularity of the roughcut model in comparison to the production scheduling model can differ greatly from manufacturer to manufacturer. Mr. Bhalla spoke of one customer that has created roughcut plans in daily buckets. In this case, the shop floor model is not all that more granular than the higher-level planning model. The plant is foregoing some degree of sequencing and setup optimization and thus also producing lower volumes.
Increasingly, manufacturers are moving away from “frozen” production plans to plans that change as demand becomes better known. A manufacturer’s production schedule for 3 weeks from now can change as the company sees surges in demand or cancelled orders. Production schedulers have visibility to the changes happening in the higher level plan and can adjust.
I asked Mr. Botha of UST how the parameters in the roughcut capacity plan and production get set. In some cases, industrial engineers with stop watches are used. But in most cases, if a consultant knows where to look, an expensive time and motion study is not necessary. “The data is there,” Mr. Botha said, “they use it for shift planning, they use it for payroll, they use it for all sorts of things, but it’s just not being used in planning.” Part of the process of getting this data involves sitting down with factory managers, understanding how items flow through the factory, and pulling data out of proprietary excel sheets they have developed.
The top floor to shop floor planning problem still exists for most manufacturers. But supply chain planning technology is getting better. It is becoming easier to overcome this chasm.
[ad_2]
Source link